Filter Press Testing Procedures
페이지 정보
작성자 Torri 댓글 0건 조회 10회 작성일 24-06-14 06:40본문
Before testing the filter press, please seek the advice of your R&B salesman to determine the forms of assessments that ought to completed for your specific utility. There are numerous filter cloths obtainable for use on a filter press and the proper choice is necessary for profitable filter press operation. Every cloth has specific traits akin to weave, porosity, thread sorts, and surface finish to achieve a stability between solids capture, cake release, blinding resistance, and cloth life. Cheremisinoff, Nicholas P. Guidebook to Mixing and Compounding Practices. Englewood Cliffs, N.J.: Prentice-Hall, 1994. Print. Geankoplis, Christie J. Transport Processes and Unit Operations. Englewood Cliffs, N.J.: Prentice-Corridor, 1993. Print. Harnby, N., M.F. Edwards, and A. W. Nienaw. Mixing in the process Industries. 2nd ed. Boston: Butterworth-Heinemann, 1992: 42, 52-fifty five, 124, 127, 132-134, 159-181, 215, 217-221, 225-247, 250-293. Print.
The pressure from the Feed Pump expels the water from the slurry, while the solids are retained inside the chambers. The number of stable cakes discharged from the filter press is decided by the number of frames, and the thickness of the cakes is dependent upon the thickness of the body. Filtering part: composed of forged iron filter plates arranged on the main beam in a certain order, and filter cloth sandwiched between the filter plates. The solid iron filter plates and filter cloth are arranged alternately, forming a number of unbiased filtering units. Pulling half: The automatic pulling part is composed of a hydraulic motor, a robotic arm, a transmission mechanism, and a suspension machine. The main characteristic of cast iron filter press is it is high temperature resistance, which is different from extraordinary filter press. The filter press plate is the primary a part of the filter press. The good high quality filter plate will enormously enhance the filter press efficiency. Filter plates embody plate frame filter plate, recessed filter plate, membrane filter plate and the special filter plate etc. The membrane filter plate is most superior.
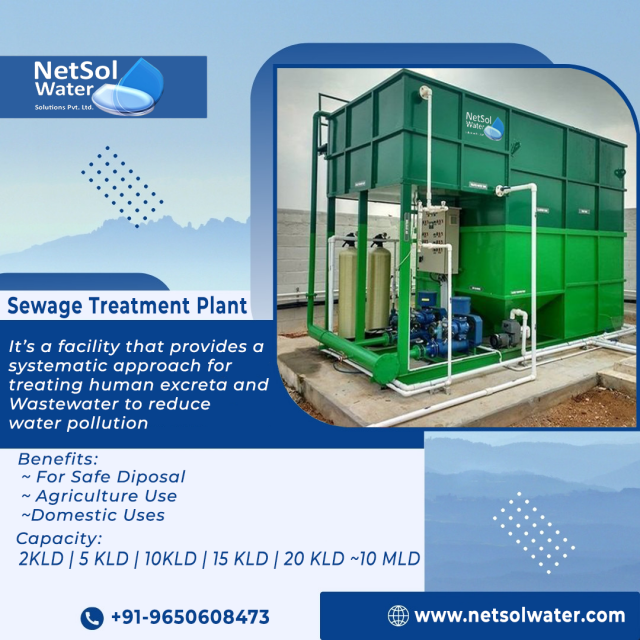
Four. Repeat step 3 to the other side of the plate. 5. Fold the one facet of the filter cloth in such a manner that it might move by the hole in the middle of the filter plate, and push the cloth by way of the plate and discard appropriately. 6. Inspect and take away any accumulated solids from the groove on both sides of the filter plate. 7. Fold one side of the new cloth in such a manner that it will possibly go by way of the opening in the middle of the filter plate, and pass the cloth through the hole in the center of the filter cloth. Eight. Aliening the brand new cloth into position by lining up the corners of the cloth to the corners of the plate. A filter press gives a easy reliable methodology of excessive compaction stress to compress and dewater solids into filter cakes of 25-60% total concentration. This offers clearer filtrate options than other filter press methods that solely remove free water. Thirty-two (32mm) millimeter gasketed polypropylene filter plates are commonplace on all models, making these heavy-responsibility filter presses effectively suited to functions, which require leak-free processing. Different standard options include a chemically resistant painted steel skeleton, 304 stainless steel bar wear strips, schedule eighty PVC head connections, four corner discharge, hydraulic closure system, and a full 6 12 months framework warranty.
Services include machining, welding, fabrication, inspection, calibration, non-destructive examination, metallurgical evaluation and testing, engineering and manufacturing know-how providers. Capabilities include lifting capacities as much as 150 tons, vertical boring as much as 20 ft. 4 in. dia. swing, radiography checking up to 15 in. 25,000 psi and laser and optical measuring. ISO 9001 compliant. Meets ASME standards. Belt filter presses are important instruments for dehydrating sludge in wastewater therapy processes. They operate by applying mechanical pressure to sludge through a sequence of progressively tighter mesh belts, successfully separating liquids from solids. In municipal wastewater management, belt filter presses are generally employed to condense the sludge generated from the biological remedy processes. As soon as the membrane squeeze step occurs, no further moisture is faraway from the cake material with further squeeze time. An instance of a membrane squeeze is shown the in dewatering curve under. How much liquid might be removed from the slurry largely will depend on the characteristics of the Best solid liquid separation machine in india material within. Feed stress and feed time additionally impact dewatering.
댓글목록
등록된 댓글이 없습니다.